社員インタビュー
.
07:45 出社 |
・メールチェック ・日報チェック |
---|
08:00 生産管理業務 |
・工場内の巡回(生産進捗チェック) ・見積りの作成 など |
---|
11:00 購買業務 |
・材料手配 ・副資材手配 |
---|
12:00 昼食 |
---|
12:45 来客対応 |
・工場内見学に同行 ・生産技術力についてのPR ・仕入業者と打合せ |
---|
16:00 品質開発業務 |
・納品物の品質管理チェック ・開発納期の資料作成 など |
---|
18:00 帰宅 |
---|
.
.
長田野工場との出会い
現在入社10年目です。私の仕事は企画の窓口で、営業と現場の間に入り仕事を橋渡しする役目をしています。客観的判断で仕事がうまく運ぶように営業と現場を結びつけるわけです。現場に近い立場なのでどうしても現場よりの考えになってしまいますが、常にそれぞれの立場で考え、中立でいる意識を持って仕事をしています。
入社当初は営業職を希望していたのですがサンキンの営業は人手が足りていたこともあり、営業にも製品の知識は必要なので、営業と技術をつなぐ企画職をやってみないかと声をかけていただいたのが今の仕事の始まりです。
実は私は文系出身でしたので、理系出身の技術職と同じ工場の勤務でもやっていけるのだろうかと思い、当時面接していただいた方にも相談してみました。すると「数字には強い方か」と尋ねられ、苦手意識はなかったので「大丈夫です」と答えたのですが、今から考えると工場勤務では部品の寸法や規格など、常に数字の羅列と接するわけですから、そのことについて質問していたんですね。それだけ、工場がどういうところか認識がない状態でのスタートでした。
3月の入社後、福知山工場の企画職として配属され3ヶ月間の現場研修最終月である、5月連休明けの第一日目に事業部長から人手の足りない長田野工場の手伝いをして欲しいと言われました。研修半ばの何もわからないままで長田野工場に勤務し、まずは製品の材料寸法をチェックし、記入していく仕事を任されました。ところが当時の長田野工場は移転したばかりで工場もやっと稼働しはじめたところ。移転しながら生産と出荷の作業も進行しなければなりません。現場は混乱していて、私の勤務一日目も営業から納期の問合せの電話が鳴り止まない大変な状況でした。まだ電話も満足に対応できないのにも関わらず、問合わせはひっきりなしにやってきます。何はともあれ鳴る電話を受け内容を控え、わからないことは現場に確認しにいく。その日は工場内を駆け回っていました。今となっては異例の待遇処置であり、いい経験となっています。
入社当初は営業職を希望していたのですがサンキンの営業は人手が足りていたこともあり、営業にも製品の知識は必要なので、営業と技術をつなぐ企画職をやってみないかと声をかけていただいたのが今の仕事の始まりです。
実は私は文系出身でしたので、理系出身の技術職と同じ工場の勤務でもやっていけるのだろうかと思い、当時面接していただいた方にも相談してみました。すると「数字には強い方か」と尋ねられ、苦手意識はなかったので「大丈夫です」と答えたのですが、今から考えると工場勤務では部品の寸法や規格など、常に数字の羅列と接するわけですから、そのことについて質問していたんですね。それだけ、工場がどういうところか認識がない状態でのスタートでした。
3月の入社後、福知山工場の企画職として配属され3ヶ月間の現場研修最終月である、5月連休明けの第一日目に事業部長から人手の足りない長田野工場の手伝いをして欲しいと言われました。研修半ばの何もわからないままで長田野工場に勤務し、まずは製品の材料寸法をチェックし、記入していく仕事を任されました。ところが当時の長田野工場は移転したばかりで工場もやっと稼働しはじめたところ。移転しながら生産と出荷の作業も進行しなければなりません。現場は混乱していて、私の勤務一日目も営業から納期の問合せの電話が鳴り止まない大変な状況でした。まだ電話も満足に対応できないのにも関わらず、問合わせはひっきりなしにやってきます。何はともあれ鳴る電話を受け内容を控え、わからないことは現場に確認しにいく。その日は工場内を駆け回っていました。今となっては異例の待遇処置であり、いい経験となっています。
.
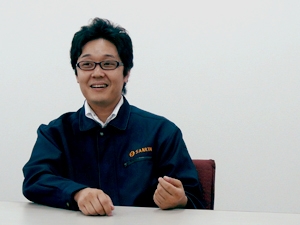
モノづくりで大事なのは「どんなモノ」を「どのように造っている」か
工場での最初の数年は傍について教えてくれる先輩もいませんでしたが、その状況は私にとってむしろ良かったのではないかと思っています。何より右も左もわからないような、新人の私に仕事に任せてもらえることや決断の機会をもらえて、さらにその決断を受け入れてくれたことがありがたく、その経験が結果として成長につながっているたのだと実感できるからです。
今でも思い出すのは、「部品の寸法とかお客様というのは常に目にするので自然に覚える、ただステンレスの知識などは自分で勉強しないと身につかない」という社長の言葉です。長田野工場で一年目だった私は、現場の仕事をこなすのに精一杯で工場における生産や納期のことばかりに集中していました。
社長からすれば、商品である自社製品の知識を自分で勉強する癖を付けさせたかったんでしょうね。それからは直接仕事に関係なくてもステンレスとはこういうものという基礎知識を身につけようと、本を買ってきたりインターネットで調べたりしてステンレスの特色や材料、溶接についてなども勉強しました。思えば面接の際上司に「文系理系は関係ない。モノづくりで大切なのは『どんなモノ』を『どのように造っている』かだ。」と言われた言葉は、まさにその通りではないかと思います。
今でも思い出すのは、「部品の寸法とかお客様というのは常に目にするので自然に覚える、ただステンレスの知識などは自分で勉強しないと身につかない」という社長の言葉です。長田野工場で一年目だった私は、現場の仕事をこなすのに精一杯で工場における生産や納期のことばかりに集中していました。
社長からすれば、商品である自社製品の知識を自分で勉強する癖を付けさせたかったんでしょうね。それからは直接仕事に関係なくてもステンレスとはこういうものという基礎知識を身につけようと、本を買ってきたりインターネットで調べたりしてステンレスの特色や材料、溶接についてなども勉強しました。思えば面接の際上司に「文系理系は関係ない。モノづくりで大切なのは『どんなモノ』を『どのように造っている』かだ。」と言われた言葉は、まさにその通りではないかと思います。
.
固定イメージを払拭したい一心での挑戦が未来を切り開いた
長田野工場で働くうちに周りの状況も見えるようになってきました。これは入社当時から感じていたのですが、長田野工場の前身となる青垣工場の頃からの「青垣スタイル」がサンキン社内に染み付いていました。
それは生産事業部の中にありながらも稼働率や注文量で第一線の生産拠点である福知山工場からは一歩引いている存在という長田野工場のイメージです。最初の2、3年はその青垣工場からの古いイメージを払拭していくことに苦労しました。
当時工場の機械は古く、メンテナンスも行きとどいていない状態でした。しかも商品の受注量が少ないため、設備投資をするにしてもなかなか実現できません。その中でも古いイメージを払拭するため良い製品を作り続けていかなければこの状況を好転させられないわけです。私がしなければならない仕事はとにかく社内での信頼を積み上げ、古いイメージを払拭し、注文量を確保すること。それしかありませんでした。
そのきっかけは突然やってきました。取引きのあったお客様が別のお客様をご紹介くださり、お引き合わせくださったのです。紹介いただいたお客様はステンレスの引抜パイプを仕入れて加工している会社だったのですが、担当者が希望される製品スペックのお話を伺ったところ、引抜加工で生産をするよりも、レーザー造管機を使って製品を造ってしまった方が早いのではという判断に至りました。とは言え未知の分野への挑戦です。「きっと造れるはずだ」と現場に頼み、できあがった試作品を元にお客様ともああでもないこうでもないと試行錯誤し、完成までには密度の濃いやり取りがありました。これがお客様の満足のいく製品として生産が実現し、製造過程を変えたことでお客様にも価格的メリットが大きい製品となりました。また、社内においても信頼を獲得でき、レーザー造管機でこんなものが造れるという長田野工場としての技術的なアピールにもなりました。はじめは大変な思いもしましたがそれでも何とかやり遂げた結果、この時に取引きさせていただいたお客様は未だに一番のお得意様なんです。
この経験がなければ今の自分はありませんし工場にとって大きな功績になったと思います。看板となるアイテムができ注文量も増えたおかげで新しい機械を導入し、長田野工場のスタイルも形になりました。そしてこの技術が全国に波及していったのは、サンキンにとって未来につながることであり、その瞬間に私自身が立ち会えた事を誇らしく思います。
それは生産事業部の中にありながらも稼働率や注文量で第一線の生産拠点である福知山工場からは一歩引いている存在という長田野工場のイメージです。最初の2、3年はその青垣工場からの古いイメージを払拭していくことに苦労しました。
当時工場の機械は古く、メンテナンスも行きとどいていない状態でした。しかも商品の受注量が少ないため、設備投資をするにしてもなかなか実現できません。その中でも古いイメージを払拭するため良い製品を作り続けていかなければこの状況を好転させられないわけです。私がしなければならない仕事はとにかく社内での信頼を積み上げ、古いイメージを払拭し、注文量を確保すること。それしかありませんでした。
そのきっかけは突然やってきました。取引きのあったお客様が別のお客様をご紹介くださり、お引き合わせくださったのです。紹介いただいたお客様はステンレスの引抜パイプを仕入れて加工している会社だったのですが、担当者が希望される製品スペックのお話を伺ったところ、引抜加工で生産をするよりも、レーザー造管機を使って製品を造ってしまった方が早いのではという判断に至りました。とは言え未知の分野への挑戦です。「きっと造れるはずだ」と現場に頼み、できあがった試作品を元にお客様ともああでもないこうでもないと試行錯誤し、完成までには密度の濃いやり取りがありました。これがお客様の満足のいく製品として生産が実現し、製造過程を変えたことでお客様にも価格的メリットが大きい製品となりました。また、社内においても信頼を獲得でき、レーザー造管機でこんなものが造れるという長田野工場としての技術的なアピールにもなりました。はじめは大変な思いもしましたがそれでも何とかやり遂げた結果、この時に取引きさせていただいたお客様は未だに一番のお得意様なんです。
この経験がなければ今の自分はありませんし工場にとって大きな功績になったと思います。看板となるアイテムができ注文量も増えたおかげで新しい機械を導入し、長田野工場のスタイルも形になりました。そしてこの技術が全国に波及していったのは、サンキンにとって未来につながることであり、その瞬間に私自身が立ち会えた事を誇らしく思います。
.
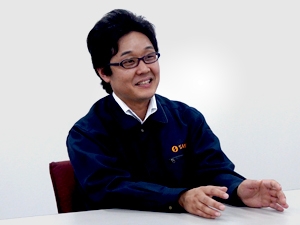
失敗を恐れず現場を体験し、自分の言葉に自信を持って欲しい
若手社員や後輩にはやはり現場を知って欲しいと思っています。それは自分自身が経験してきたことだからこそ言えるのですが、どんな職種であろうとも現場で自分が体感したことは裏付けされた経験として自信を持って答えられますし、それは経験をしていない人にはできないことだと思うからです。
自社で製造可能な範囲は把握しよく理解しておく。その上で範囲外だが何とか生産ができないだろうかと現場に掛け合ってみる。
よく失敗したらどうしようと自己ブレーキをかけ怒られないように振る舞い、言われたら言われたことだけをしているような人がいますが、私は成功のために失敗はつきものだという認識でいます。それを工場で学びました。
ものづくりの過程では一度で成功する仕事はほとんどありません。そういう意味でも失敗を恐れないという気持ちを持てるかどうかは重要になってきます。失敗と修正、トライアンドエラーを繰り返し目標を達成していくんです。
もちろん、ミスを防ぐための取り組みや努力はしなければいけません。ただ私自身は失敗をしたときにあきらめるのではなく成長してやろうという気持ちを持って取り組んでいますし、その経験でここまでやって来れたと思っています。
サンキンは自分からチャレンジしていける社風なので、是非新入社員の方にも、失敗を恐れない心を持って成長していってほしいですね。
自社で製造可能な範囲は把握しよく理解しておく。その上で範囲外だが何とか生産ができないだろうかと現場に掛け合ってみる。
よく失敗したらどうしようと自己ブレーキをかけ怒られないように振る舞い、言われたら言われたことだけをしているような人がいますが、私は成功のために失敗はつきものだという認識でいます。それを工場で学びました。
ものづくりの過程では一度で成功する仕事はほとんどありません。そういう意味でも失敗を恐れないという気持ちを持てるかどうかは重要になってきます。失敗と修正、トライアンドエラーを繰り返し目標を達成していくんです。
もちろん、ミスを防ぐための取り組みや努力はしなければいけません。ただ私自身は失敗をしたときにあきらめるのではなく成長してやろうという気持ちを持って取り組んでいますし、その経験でここまでやって来れたと思っています。
サンキンは自分からチャレンジしていける社風なので、是非新入社員の方にも、失敗を恐れない心を持って成長していってほしいですね。
.
.